Case studies / Altenloh, Brinck & Co.
Altenloh, Brinck & Co. U.S. Gets DymaxIO
Solves Critical ERP System Bottleneck to Speed Order Processing and Shipping
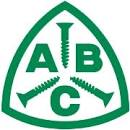
“Our people are no longer a day behind. With DymaxIO, our ERP system runs so much faster, we process and ship all of our orders on the same day.”
CURT HAPNER
CHIEF INFORMATION OFFICER
ALTENLOH, BRINCK & CO. U.S.
Challenges
- New Epicor ERP system created backend bottleneck, causing significant decline in productivity
- Order processing was slow, causing shipping delays of at least one day
- Increased SQL “wait” times for application response, data processing
- Days and weeks of IT resources spent troubleshooting and fighting fires
Benefits
- 50% or greater application performance improvement – with no additional hardware
- Latency and throughput dramatically improved
- True “set and forget” management
- Compatible with all SAN/NAS systems
- Easily deploys to the largest virtual, physical or cloud environments in just five clicks
- Before-and-after performance reporting to validate performance gains
- Enterprise-wide visibility into I/O performance, from VM to storage
Environment
- VMware® ESX and ESXi
- SAN Technology: HP LeftHand P4500®
- Epicor ERP software
- SQL Server
Features
IntelliWrite® automatically prevents split I/Os from being generated when a file is typically broken into pieces before write and sequentializes otherwise random I/O generated by the “I/O blender” effect.
IntelliMemory® intelligent caching technology caches active data from read requests using available server memory.
“Time Saved” Benefits Dashboard Shows the ongoing benefit of the software by revealing the amount of I/O offloaded from storage and how much time that saves.
Benefit Analyzer™ embedded benchmark provides before/after performance comparisons prior to installing DymaxIO and after
When Altenloh, Brinck & Co. U.S. added a new ERP system for efficient supply chain management, the result was an unexpected strain from I/O demand, causing system crashes, data corruption, and handheld scanners locking up. Orders were processing so slowly, shipping was behind by at least a day.
THE CUSTOMER
ALTENLOH, BRINCK & CO. U.S., INC., (ABC U.S.) is the manufacturer of the TRUFAST® and SPAX® brands of engineered fastening solutions for the commercial roofing and residential construction industries.
THE CHALLENGE
Manufacturing, warehousing, and shipping a variety of packaged inventory to different market channels comes with inherent challenges, but when ABC U.S. added Epicor for enterprise resource planning (ERP), IT took an unexpected hit. “Our TRUFAST commercial roofing business segment went online in April 2012, followed by the SPAX business in January, 2013,” says Curt Hapner, Chief Information Officer. “Adding a new ERP package put a huge burden on our SAN and virtual infrastructure systems, as we started shoving large datasets back and forth across the network.”
Using monitoring tools, Curt could see SQL “waits” increasing, whether it was wait times to access the database or wait times for Epicor to grind through business logic. But from the perspective of his associates, the issues were worse than long wait times. “Our associates were getting out-of-memory alerts, clients and devices crashing—and our warehouse management piece is another story,” he explains. “I support two large warehouses, SPAX and TRUFAST, each running multiple remote devices. So our hand-held scanners wouldn’t work, and printing pack lists would kill the system and corrupt the data tables.” He continues, “I had someone dedicated full-time to cleaning the data tables due to all the lock-ups and crashes.”
According to Curt, ABC U.S.’s transaction process was like a snake swallowing a softball. “We would piecemeal orders because the system couldn’t handle too many at once. It would take one person a full day to walk orders through the cycle—from sales to shipping.” At that pace, the shipping team wouldn’t receive orders until quitting time, delaying shipments by at least one day.
THE SOLUTION
Working with Condusiv’s pre-sales team, Curt was able to run DymaxIO® on several VMs, looking for improvements in workload processing. “We hadn’t even purchased DymaxIO yet, and we had full access to support. The ease of getting up and running was excellent,” he explains. “We tested the waters and, once I was confident nothing was blowing up, we pushed DymaxIO to the ERP hosts. I wanted to see the results in context of our biggest trouble spots before making a decision to purchase.”
Curt collected feedback from various business units, verifying DymaxIO’s impact. “Within days, I had reports back from shipping that scanners were no longer locking up, and there hadn’t been any system crashes,” he says. “That’s all the verification I needed.”
ABC U.S. had recently tuned their HP LeftHand SAN, but adding demand from a new ERP system brought SQL and application performance to a standstill. Installed on Windows VMs at the operating system layer, DymaxIO nondisruptively optimizes I/O at the source—reducing the I/O requirement for all files. By preventing a surplus of I/O from getting funneled into servers, network, and storage, the entire infrastructure (computer, network, and storage) derives benefit because only productive I/O is generated by the VM.
With IntelliWrite technology, Condusiv automatically prevents split I/Os from being generated, allowing more data to be packaged on every write. With IntelliMemory, DymaxIO caches active data in available server memory to further reduce I/O demand on storage devices.
THE RESULT
ABC U.S. struggled with a process constantly interrupted by system crashes and people unable to perform basic job functions. With team members standing idle until late afternoon, waiting to “pick and pack” orders for shipping, the backend bottleneck was critical—impacting supply chain management, labor, and productivity.
“We were looking at adding more hardware and hoping for the best,” Curt says. “We did finally add more VMs to split up the load, but it had no impact. It had nothing to do with the application, but the volume of I/O going through the system,” he explains.
Since rolling out DymaxIO, there have been no system crashes, device lock-ups, and corrupted data tables. The IT resource dedicated to fighting fires is now doing the job she was hired for.
“By getting rid of I/O, DymaxIO solved our problems, and I saved about $250K in hardware costs,” he explains. “Performance has improved so significantly, orders move from sales to shipping in real-time, saving a day of productivity. Now our biggest problem is we can hardly keep up with the pace of the orders. We’re more efficient than ever and people are back to loving their jobs.”